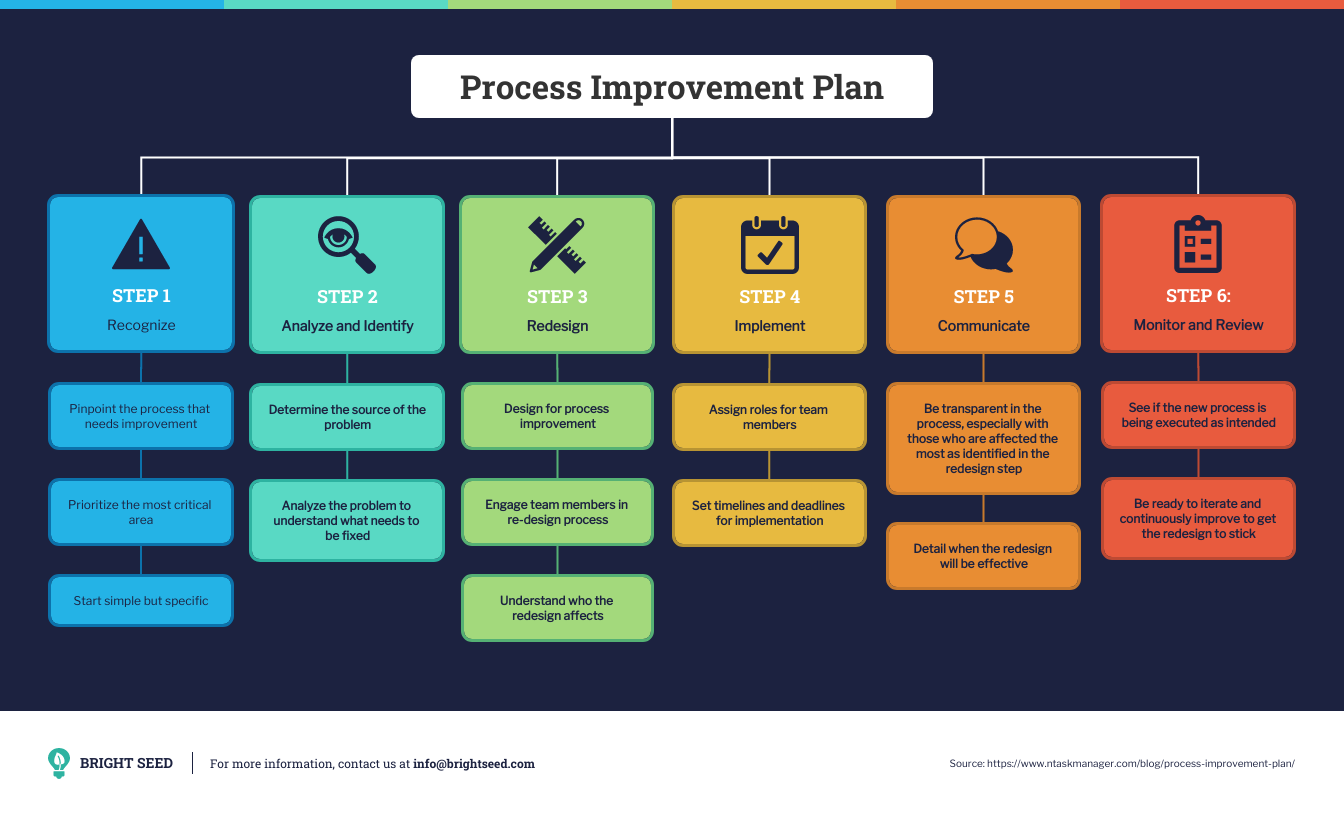
In today’s competitive business world, organizations are constantly striving to improve their operations and processes to stay ahead of the game. Operations and process improvement is the practice of analyzing and enhancing the efficiency, productivity, and effectiveness of a company’s operations to maximize its overall performance.
The Importance of Operations and Process Improvement
Operations and process improvement plays a crucial role in the success of a business. It allows organizations to identify and eliminate inefficiencies, reduce costs, increase customer satisfaction, and improve overall performance. By continuously evaluating and refining their processes, companies can streamline their operations, optimize resource utilization, and enhance their competitive advantage.
Key Benefits of Operations and Process Improvement
Enhanced Efficiency: By eliminating unnecessary steps and automating manual tasks, operations and process improvement boosts efficiency and reduces the time required to complete tasks.
Reduced Costs: Streamlining operations and eliminating waste helps reduce costs associated with inefficiencies, such as excess inventory, unnecessary labor, and rework.
Improved Quality: Process improvement methodologies, such as Six Sigma and Lean, focus on reducing defects and errors, leading to improved product and service quality.
Increased Customer Satisfaction: Optimized processes result in faster delivery, fewer errors, and better overall customer experience, leading to higher customer satisfaction and loyalty.
Higher Productivity: Improved processes, automation, and the elimination of bottlenecks contribute to increased productivity and output.
Better Decision Making: Through data analysis and process optimization, operations and process improvement provides organizations with valuable insights for making informed and data-driven decisions.
Popular Operations and Process Improvement Methodologies
There are several methodologies and frameworks commonly used for operations and process improvement:
Six Sigma: Six Sigma focuses on reducing defects and minimizing process variations by using statistical analysis and data-driven decision-making.
Lean Manufacturing: Lean manufacturing aims to eliminate waste, improve flow, and enhance value through continuous improvement and the elimination of non-value-added activities.
Total Quality Management (TQM): TQM is a holistic approach that emphasizes the involvement of all employees in quality improvement, aiming for the highest level of customer satisfaction.
Business Process Reengineering (BPR): BPR involves the radical redesign of processes to achieve significant improvements in cost, quality, service, and speed.
Implementing Operations and Process Improvement
Implementing operations and process improvement requires a systematic approach. Here are some key steps:
Identify Areas for Improvement: Conduct a thorough analysis of existing processes to identify bottlenecks, inefficiencies, and areas of improvement.
Set Clear Goals and Objectives: Define specific, measurable, achievable, relevant, and time-bound (SMART) goals to guide the improvement efforts.
Engage Employees: Involve employees at all levels in the improvement process, encouraging their active participation, input, and feedback.
Analyze Data: Collect and analyze data to identify patterns, trends, and areas of improvement. Use tools such as process mapping, root cause analysis, and data visualization techniques.
Develop and Implement Improvement Strategies: Based on the analysis, develop improvement strategies and action plans. This may involve reengineering processes, introducing new technology, or implementing quality control measures.
Monitor and Evaluate: Continuously monitor the implemented improvements and evaluate their effectiveness. Make necessary adjustments to ensure sustained improvement over time.
Continuous Improvement Culture: Foster a culture of continuous improvement by encouraging ongoing evaluation and innovation.
Conclusion
Operations and process improvement is essential for organizations looking to enhance their competitiveness, maximize efficiency, and improve customer satisfaction. By adopting the right methodologies, involving employees, and continuously analyzing and refining processes, businesses can achieve significant improvements in their operations. Embracing a culture of continuous improvement ensures long-term success and growth.
Written by: Your Name